The State of Data Operations in Asset-Intensive Industries
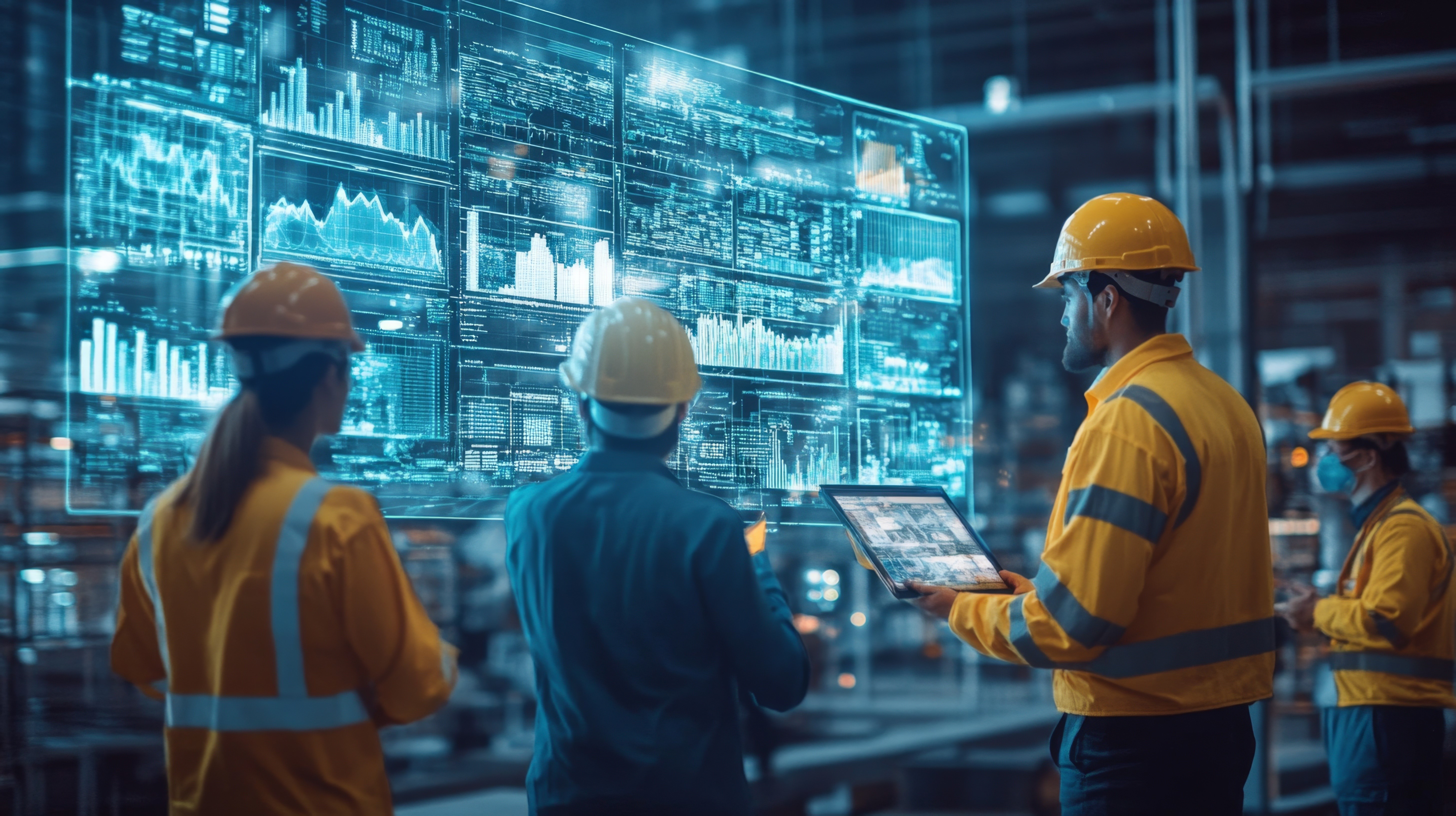
Thirteen years ago, at a fair in Hanover, Germany, the term “Industry 4.0” entered the industrial lexicon. The timing was fitting. The HTC Evo had just launched as the first 4G phone and 30% of Americans had adopted smartphones. Digital transformation was the buzzword of the day and the vision of smart factories with autonomous, data-driven machines seemed to be only years away.
Fast forward to today, and that vision is slowly becoming reality. Across the industry, companies are taking steps to digitize operations and unlock the potential of their data. But the path to Industry 4.0 is a spectrum - some factories deploy cutting-edge ML and others still rely on clipboards to track production.
Over the past few months, the Dime team has spoken to dozens of manufacturing and data engineers, and here’s what we’ve learned about where the industry stands today.
The Current Landscape of Data Operations
The reality for many manufacturers is shaped by legacy equipment. Machines purchased decades ago often lack the sensors or connectivity to generate meaningful data, let alone feed it into modern systems. American manufacturing’s slowdown since the 1970s left many plants with infrastructure built for a different era. Yet, despite these challenges, some industries—particularly those with continuous operations like oil & gas, chemicals, and food & beverage—are much further along in their digital journeys. These companies have the most to gain from incremental improvements, where even a 1% increase in efficiency can mean millions in savings.
In contrast, discrete manufacturers, like medical device companies with human-driven assembly stations, are often able to spot issues through observation and experience. For them, the urgency to invest in data operations isn’t as strong. As a result, the maturity of data operations varies widely across industries and even within companies.
Stages of Digital Transformation
Manufacturers tend to fall into one of four stages on their data operations journey:
- Production Tracking with Basic Data Extraction
For most manufacturers, the first step is understanding what’s happening on the factory floor. In the past, whiteboards and clipboards were the go-to tools, but they’re impractical for real-time insights in a 100K+ square foot facility. Modern machine monitoring tools now fill this gap, enabling plant managers to track production remotely. Even older machines can be retrofitted with voltage sensors to estimate cycle counts. It’s not perfect, but it’s a start. - Flexible Visualizations
Companies with connected assets are finding new ways to visualize their operations. Tools like PowerBI have become invaluable, allowing manufacturing teams to create dashboards that transform raw data into actionable insights. By leveraging historians, manufacturers can track performance and identify bottlenecks. However, these tools often require the expertise of BI analysts to unlock their full potential. - Retroactive Analysis with Data Engineers
The most advanced manufacturers take things further, employing teams of data engineers to analyze historical data and identify opportunities for improvement. Moving data from on-prem historians to the cloud opens up new possibilities for analysis and optimization. For companies running 24/7 operations, even small improvements in yield or uptime can have a massive impact on the bottom line. - Automated Real-Time Optimization
At the top of the pyramid are companies that have mastered their infrastructure and are deploying machine learning models in real time either natively in their control systems or utilizing technology like OPC UA. These teams can extract actionable insights in real-time, enabling immediate adjustments through closed feedback loops integrated directly into control systems. While this level of sophistication remains rare, it sets the standard for what’s possible and offer a glimpse into the future for manufacturers with the resources to invest.
The Problem with the Status Quo
Despite the progress, most manufacturers are locked out of advanced data operations. The cost of integration for top-end platforms can run into the millions, and hiring the specialized talent to make sense of the data adds an ongoing operating expense. This creates a gulf between the largest players, who have the resources to innovate, and everyone else, who are left behind.
Can GenAI Actually Help?
This is where GenAI has the potential to change everything. By automating complex data transformations, it can drastically reduce the time and cost of integrating advanced tools. More importantly, it can democratize access to insights. With innovations like text-to-SQL and context-based query generation, manufacturing and process engineers can interact with their data directly—no data science team required.
At Dime, we’re building tools to make this vision a reality. Our platform bridges the gap, enabling manufacturers of all sizes to extract value from their data without breaking the bank.
The dream of Industry 4.0 was never just about technology. It’s about creating a future where every manufacturer—big or small—can run smarter, leaner, and more connected operations.
Ready to unlock the potential of your data? Schedule a demo and let’s explore how Dime can empower your operations.